1- Çeliğe Şekil Verilmesi İhtiyacı
Teknolojinin ve metalürji biliminin gelişmesi ile günümüz koşullarında, seri üretim yapan sanayi sektörlerinin kapasiteleri ve kullandıkları malzeme türleri ve şekilleri değişime uğramaktadır. Yeni ara ve tam mamul ürünler için gerekli şekillendirme işlemleri kapsamında yüksek sıcaklıklara ihtiyaç duyulmakta ve bu sıcaklıklarda malzemelere farklı bir form kazandırılmaktadır. Bu süreçte ilgili malzemelere istenen şekil verildikten sonra soğutulma sürecine geçilebilir.
2- Sıcak Haddeleme Nedir?
Çeşitli metallere veya farklı metallerin bir arada kullanılması ile oluşturulan alaşımlara yüksek sıcaklıklarda yapılan deformasyon işlemi sıcak haddeleme olarak ifade edilir. Bu deformasyon işleminde, ilgili malzemelerin kırılmaya ya da kopmaya karşı dayanıklılıklarını ifade eden sünekliliklerinin yüksek olduğu yeniden kristalleşme için gerekli yüksek sıcaklıklar tercih edilir. Sıcak hadde kavramı için metale uygulanan sıcak ve soğuk işlemler ile şekillendirme denebilir. Sıcak haddelenmiş çelik malzemeye daha keskin boyut ve hassas yüzeyler kazandırılması için ilave işlemler yapılır. Bu işlemler soğuk haddeleme olarak bilinir ve sıcak haddeleme sonrasında çeliğe uygulanır.
3- Sıcak Haddeleme Süreci
Sıcak haddelenmiş çelik yapım sürecinde çelik malzeme yüksek sıcaklıklar uygulanan fırınlarda sıvı cevher haline getirilir ve slab adı verilen kalıplara dökülür. Sıcak haddelenmiş çelik özellikleri ve formu korunabilmesi amacıyla belirli aşamalarda basınçlı su kullanılarak yüzey arındırılması yapılır. Haddeleme sürecinde çelik kütükler haddehanedeki 1200-1400 derece arasındaki tavlama ocaklarında işlem görür. Tavlanan malzemelere tamburlar ve döner merdaneler yardımıyla uygulanan baskı neticesinde kalınlık 0.4-0.6 mm’ye kadar düşürülür. Haddeleme sonrasında uç kısımlarda oluşan dengesiz uzamalar kesilir.
4- İnceltme İşlemleri
Sıcak haddeleme işlemi genel hatlarıyla tamamlandıktan sonra inceltme işlemi farklı çalışma ortamlarında değişik şekillerde yapılabilir. Bu noktada, haddeleme iki merdane arasında git gel yapılarak tamamlanabileceği gibi art arda sıralanmış tamburlarda da tek seferde de yapılabilir. Her iki yönteminde son aşamasında soğutulma işlemi yapılır ve istenen hale getirilen malzemeler paketlenir.
5- Sıcak Haddeleme ve Soğuk Haddeleme Maliyetleri
Sıcak haddeleme ve soğuk haddeleme işlemlerinden sıcak haddeleme, çelik bir malzemeye uygulanan ilk işlemler olarak kabul edilebilir. Genel hatlarıyla yapılan bu işlemlerde ortaya çıkan malzemeler kalın olduğu için hassas uygulamalara uygun değildir. Sıcak haddelemede malzemeye daha az işlem uygulandığı için sıcak haddelenmiş çeliğin maliyeti daha düşük olur. Dolayısıyla soğuk haddeleme ürünlerin maliyetinde işlem çokluğuna bağlı olarak artış yaşanacaktır. Sıcak haddeleme sonrası elde edilen malzeme, sertleştirme sürecinde oluşabilecek iç gerilmelerden arındırılmak için, oda sıcaklığında soğutma işlemine bırakılır.
6- Sıcak ve Soğuk Hadde Farkı
Çeliğe, kalınlık ve genişlik toleranslarını azaltmak ve detay kazandırmak amacıyla daha fazla işlem yapıldığında sıcak hadde soğuk hadde farkı ortaya çıkar. Sıcak haddelenmiş çeliğin detayları az olduğu için kaba inşaat işlerinde veya tren raylarında tercih edilmektedir. Buradan hareketler sıcak haddelenmiş çelikler yüzey kaplamaya ihtiyaç duyulmadığı durumlarda daha çok tercih edilir. Yüzey kalitesinin artırılmak istendiği hallerde söz konusu malzemeye taşlama, kumlama ve asit banyosu uygulanabilir. Bu sayede çelik malzeme kireçten de arındırılmış olur ve neticede boya ve yüzey kaplama gibi işlemlere uygun hale getirilir.
7- Haddeleme Yapılarak Üretilen Ürünler
Sıcak haddeleme ile mamul ürünler ve detay gerektirmeyen kaba ürünler üretilir. Bu ürünler kare, dikdörtgen, çokgen, yuvarlak ve yassı olabileceği gibi demir çubuk şeklinde de olabilir. Ayrıca sıcak haddelenmiş çelikler otomotiv sektöründe jant ve şasi parçalarının üretimi için kullanılır. Süneklik ve tokluk optimizasyonu sağlanması akabinde inşaat çeliklerinde, yapı levhalarında, iş makinelerinde, depolama tanklarında ve konteyner üretiminde kullanılır.
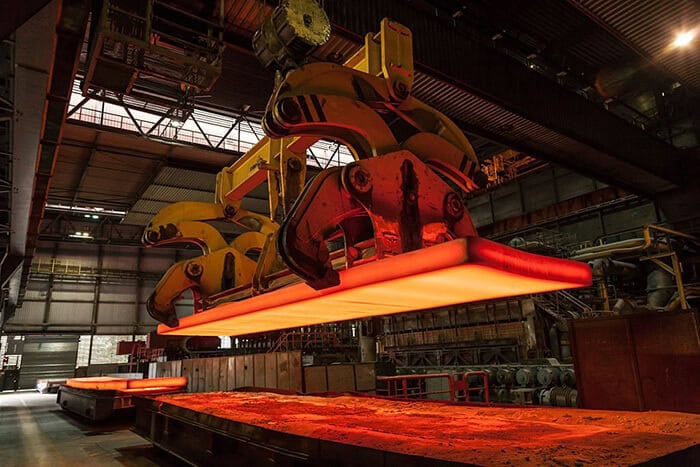